5 Latest Trends In Warehousing Technologies
In the ever-evolving landscape of logistics and supply chain management, the adoption of advanced warehousing technologies has become a critical factor in staying competitive and efficient. As industries strive to streamline their operations and enhance overall productivity, the integration of cutting-edge technologies into warehouse management processes has become a necessity. This blog will delve into the transformative impact of advanced warehousing technologies, exploring the key innovations and their implications for the future of supply chains.
Automated Guided Vehicles (AGVs) and Robotics
One of the most prominent advancements in warehousing technology is the widespread use of Automated Guided Vehicles (AGVs) and robotics. AGVs are autonomous mobile robots that navigate through warehouses using predefined routes, efficiently transporting goods from one location to another. Robotics, on the other hand, play a crucial role in automating various tasks within the warehouse, such as picking, packing, and sorting.
Automated Guided Vehicles (AGVs)
Autonomous Mobility: AGVs are self-guided vehicles equipped with sensors, cameras, and other navigation technologies that enable them to move autonomously within a warehouse or facility.
Navigation Systems: AGVs typically use various navigation systems, such as laser guidance, magnetic strips, or vision-based systems, to follow predefined paths or navigate around obstacles in real-time.
Efficient Material Handling: AGVs are designed to transport goods and materials from one location to another, reducing the need for manual labor in material handling tasks. This can include transporting pallets, bins, or other containers within the warehouse.
Flexibility: AGVs can be programmed and reprogrammed easily to adapt to changes in the warehouse layout or workflow, providing a high degree of flexibility.
Robotics
Task Automation: Robotics in warehousing involves the use of robotic systems to automate various tasks traditionally performed by human workers. This includes tasks such as picking, packing, sorting, and even some aspects of inventory management.
Pick and Place Robots: Robots equipped with robotic arms and grippers are capable of picking items from shelves or containers and placing them at designated locations. This is particularly beneficial in e-commerce fulfillment centers with a high volume of individual item orders.
Sorting Systems: Robots can be employed in sorting centers to categorize and organize items based on predefined criteria. This improves the speed and accuracy of order fulfillment processes.
Collaborative Robots (Cobots): Some robotic systems are designed to work alongside human workers, enhancing collaboration and efficiency. These cobots can assist with tasks that require a combination of human dexterity and robotic precision.
Benefits of AGVs and Robotics in Warehousing
Increased Efficiency: AGVs and robotics accelerate warehouse operations, reducing the time required for tasks like material handling, picking, and packing.
Error Reduction: Automation minimizes the risk of human errors, leading to higher accuracy in tasks such as order fulfillment and inventory management.
24/7 Operations: AGVs and robots can operate continuously, contributing to round-the-clock warehouse productivity without the limitations of human working hours.
Labor Optimization: By automating repetitive and labor-intensive tasks, organizations can optimize human labor for more complex and strategic roles.

Warehouse Management Systems (WMS)
Warehouse Management Systems (WMS) have evolved into sophisticated platforms that orchestrate and optimize a wide array of warehouse activities. These systems integrate with other technologies, providing a centralized hub for managing inventory, order fulfillment, and overall warehouse operations. Here are some key aspects to further elaborate on the functionalities and benefits of WMS:
Inventory Management
- WMS provides real-time visibility into inventory levels and locations. This helps in preventing stockouts, overstock situations, and allows for efficient order fulfillment.
- Automated tracking of inventory movements, including receiving, picking, packing, and shipping, ensures accurate stock levels and reduces the risk of errors.
Order Fulfillment
- WMS helps optimize the order picking process by providing intelligent picking routes, reducing travel time, and improving overall efficiency.
- Order accuracy is enhanced through barcode scanning and other technologies, minimizing errors in shipment.
Space Optimization
- WMS assists in maximizing warehouse space utilization by providing insights into the best storage locations for different types of products.
- It helps in organizing inventory based on factors like turnover rates, product dimensions, and storage requirements.
Automation of Routine Tasks
- Routine tasks such as data entry, order processing, and inventory tracking can be automated through WMS, reducing manual labor and minimizing human errors.
- Automation also speeds up processes, allowing for quicker turnaround times and improved overall efficiency.
Integration with Other Technologies
- WMS often integrates with other technologies such as barcode scanning, RFID (Radio-Frequency Identification), and IoT (Internet of Things) devices to enhance data accuracy and real-time tracking.
- Integration with ERP (Enterprise Resource Planning) systems ensures a seamless flow of information between different business functions.
Traceability and Visibility
- WMS enables end-to-end traceability of products in the supply chain. This is crucial for compliance, quality control, and recalling products if necessary.
- Real-time visibility into the movement of goods allows for better decision-making and responsiveness to changes in demand or supply chain disruptions.
Reporting and Analytics
- WMS generates detailed reports and analytics on key performance indicators (KPIs) such as order fulfillment rates, inventory turnover, and workforce productivity.
- These insights empower warehouse managers to make data-driven decisions and continuously improve warehouse operations.
Scalability and Adaptability
WMS systems are designed to be scalable, accommodating the growth of businesses over time. They can adapt to changing warehouse layouts, inventory types, and order volumes.
You Might Also Like To Read: How to choose the right warehouse management software?

Artificial Intelligence (AI) and Machine Learning (ML)
AI and ML technologies are transforming the way warehouses operate by enabling predictive analytics and intelligent decision-making. AI algorithms analyze historical data to predict demand patterns, allowing warehouses to optimize inventory levels and reduce excess stock. ML algorithms also enhance the accuracy of demand forecasting, helping businesses align their inventory with actual market needs.
Moreover, AI-powered systems can optimize picking routes, reducing travel time and improving overall order fulfillment speed. By continuously learning from data, these technologies adapt to changing trends and demands, making warehouses more agile and responsive.
Benefits of AI and ML
Demand Forecasting and Inventory Optimization
Historical Data Analysis: AI algorithms leverage historical data, including sales patterns, market trends, and external factors, to predict future demand accurately. This allows warehouses to proactively manage inventory levels, ensuring that they stock the right quantity of products to meet customer demand without overstocking.
Reduced Excess Stock: By understanding and forecasting demand more precisely, AI helps warehouses optimize their inventory levels. This optimization reduces excess stock, mitigates carrying costs, and minimizes the risk of obsolescence. Warehouses can maintain a leaner and more cost-effective inventory, freeing up capital for other strategic initiatives.
Enhanced Demand Forecasting Accuracy
Machine Learning Algorithms: ML algorithms play a crucial role in enhancing the accuracy of demand forecasting. These algorithms continuously learn from new data, adapting to changing market conditions and consumer behavior. As a result, the demand forecasts become more refined and reliable over time, enabling warehouses to make informed decisions regarding procurement and inventory management.
Dynamic Adaptation: ML algorithms can dynamically adapt to various factors influencing demand, such as seasonality, promotions, or external events. This adaptability ensures that warehouses can respond swiftly to changing market dynamics, preventing stockouts during peak demand periods and avoiding overstocking during slow seasons.
Optimized Picking Routes and Order Fulfillment
Route Optimization: AI-powered systems analyze data related to warehouse layouts, inventory locations, and order requirements to optimize picking routes. By considering factors like item popularity, proximity, and order priorities, these systems design the most efficient paths for warehouse workers or automated robots. This minimizes travel time, reduces congestion, and improves overall order picking efficiency.
Improved Order Fulfillment Speed: AI-driven optimization extends beyond picking routes to enhance overall order fulfillment speed. By intelligently managing resources and prioritizing orders based on factors like delivery deadlines, AI ensures that high-priority orders are processed quickly. This not only enhances customer satisfaction but also contributes to a more agile and responsive warehouse operation.
Continuous Learning and Adaptation
Adaptive Algorithms: AI and ML systems operate on adaptive algorithms that learn from real-time data. This continuous learning process enables warehouses to stay ahead of market trends, customer preferences, and operational challenges. The system becomes more adept at recognizing patterns, anomalies, and opportunities, contributing to a warehouse’s ability to adapt to evolving business landscapes.
Data-Driven Decision-Making: AI facilitates data-driven decision-making by providing actionable insights based on real-time and historical data analysis. This empowers warehouse managers to make informed choices regarding inventory levels, resource allocation, and process improvements. The result is a more agile and responsive warehouse that can proactively address challenges and seize opportunities.
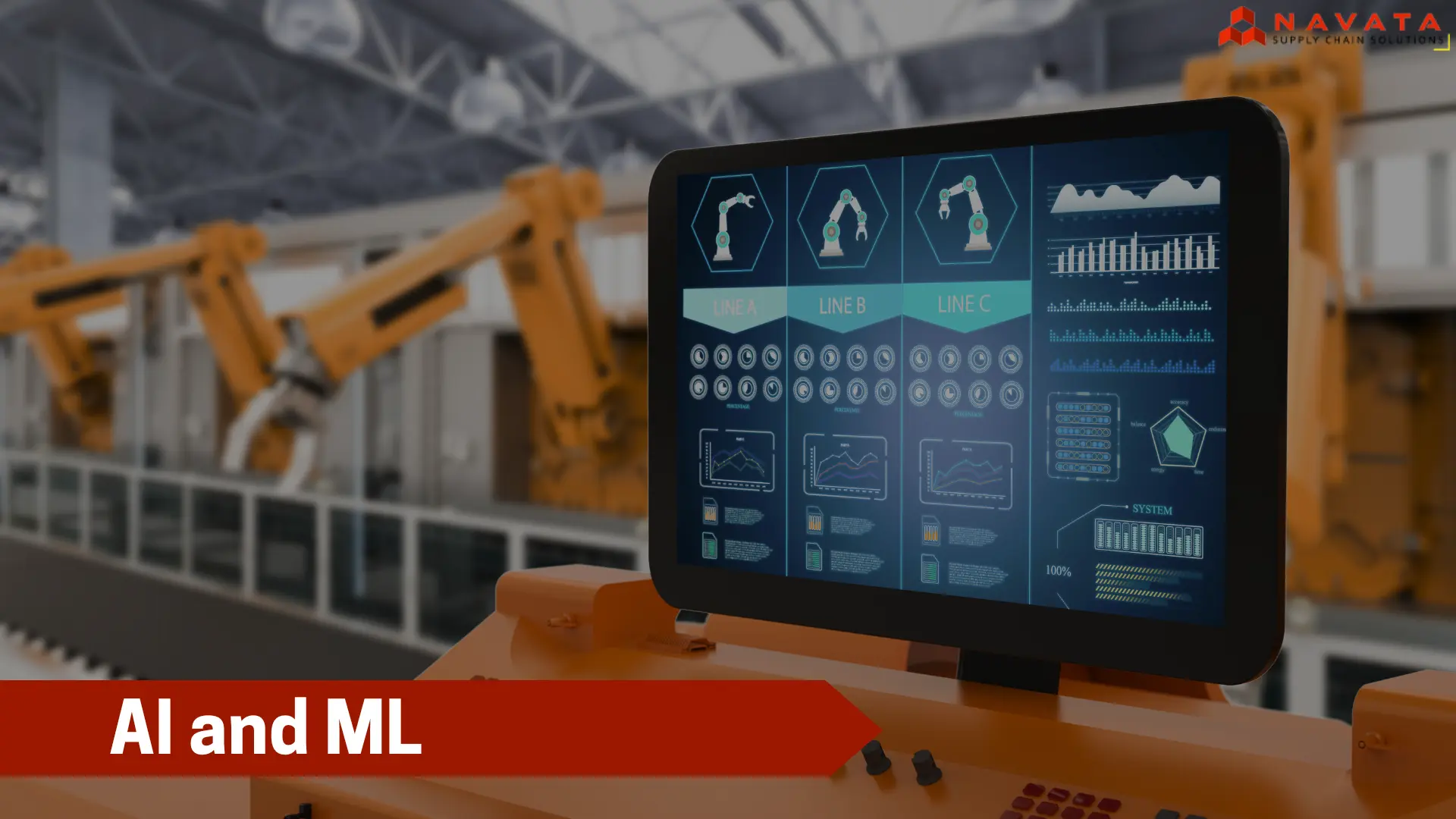
IoT-enabled Smart Warehouses
The Internet of Things (IoT) has brought about a paradigm shift in warehouse management by enabling the creation of smart warehouses. IoT sensors and devices are strategically placed throughout the warehouse to collect real-time data on various parameters such as inventory levels, environmental conditions, and equipment status.
By leveraging IoT, warehouses can attain unprecedented visibility into their operations, allowing for proactive decision-making and predictive maintenance. This not only minimizes the risk of stockouts or overstock situations but also ensures the integrity of sensitive products through continuous monitoring of storage conditions.
Benefits of IoT-enabled Smart Warehouses
Real-time Visibility: IoT sensors provide real-time data on inventory levels, equipment status, and environmental conditions, offering unparalleled visibility into warehouse operations.
Proactive Decision-Making: With continuous data streaming from IoT devices, warehouse managers can make proactive decisions to optimize workflows, prevent stockouts, and respond swiftly to changes in demand or supply chain disruptions.
Predictive Maintenance: IoT enables predictive maintenance by monitoring the condition of equipment in real-time. This helps in identifying potential issues before they lead to equipment failures, reducing downtime and maintenance costs.
Optimized Inventory Management: Real-time tracking of inventory through IoT sensors ensures accurate and up-to-date information. This optimizes inventory management, preventing overstock and stockouts, and improving overall warehouse efficiency.
Environmental Monitoring: IoT sensors can monitor environmental conditions such as temperature and humidity. This is crucial for warehouses storing sensitive goods like pharmaceuticals or perishable items, ensuring their quality and integrity.
Enhanced Security: IoT-enabled smart warehouses often incorporate security features like surveillance cameras and access control systems. These contribute to improved warehouse security by monitoring activities and preventing unauthorized access.
Efficient Resource Utilization: By analyzing data from IoT devices, warehouses can optimize the utilization of resources, including labor, equipment, and storage space. This leads to increased efficiency and cost savings.

Drones in Warehousing
Drones are increasingly finding applications in warehousing, particularly in large facilities with extensive inventory. These unmanned aerial vehicles are used for inventory counting, monitoring storage conditions, and even transporting small, high-priority items within the warehouse.
The use of drones in warehousing reduces the time and resources required for manual inventory checks and provides a swift and accurate means of data collection. As technology continues to advance, drones are expected to play a more integral role in optimizing warehouse logistics.
Benefits of Drones in Warehousing
Efficient Inventory Management
- Drones can quickly and autonomously navigate through large warehouses to perform inventory checks. This process is significantly faster than traditional manual methods, reducing the time and labor required for inventory management.
- Real-time data collection allows for more frequent and accurate inventory counts, enabling better decision-making and minimizing the risk of stockouts or overstock situations.
Time and Cost Savings
- Automation of inventory checks through drones leads to substantial time savings. This efficiency allows warehouse staff to focus on more value-added tasks, such as analyzing data, optimizing processes, and addressing exceptions.
- Reduced labor costs associated with manual inventory checks contribute to overall cost savings for warehouse operations.
Enhanced Accuracy
- Drones are equipped with advanced sensors and cameras, providing high levels of accuracy in data collection. This minimizes the likelihood of errors that can occur during manual inventory counts, leading to improved overall inventory accuracy.
- Accurate inventory data is crucial for preventing stockouts, avoiding excess inventory, and ensuring that the right products are available when needed.
Monitoring Storage Conditions
- Drones can be equipped with sensors to monitor environmental conditions within the warehouse, such as temperature and humidity. This is particularly important for warehouses storing goods that require specific climate conditions.
- Early detection of issues such as temperature variations or leaks allows for prompt corrective action, preventing potential damage to inventory.
Swift and Flexible Transportation
- Drones can be utilized to transport small, high-priority items within the warehouse quickly. This is especially valuable for items that need to be delivered urgently or for optimizing the movement of goods in a just-in-time production environment.
- The flexibility of drone transportation can contribute to faster order fulfillment and improved overall warehouse efficiency.
Scalability
Drones are scalable and can adapt to the size and layout of different warehouses. Whether a warehouse is large or small, drones can efficiently cover the entire space, providing a scalable solution for inventory management and monitoring.
Technology Integration
The integration of drone technology with warehouse management systems (WMS) allows for seamless communication and data exchange. This integration ensures that the information collected by drones is directly utilized for decision-making and process optimization.

Thanks For Reading: Advanced Warehousing Technologies: 5 Latest Trends
Powered By 360Presence
6 Comments
Kandi
great submit, very informative. I wonder why the other experts
of this sector don’t notice this. You must continue your writing.
I am sure, you have a great readers’ base already!